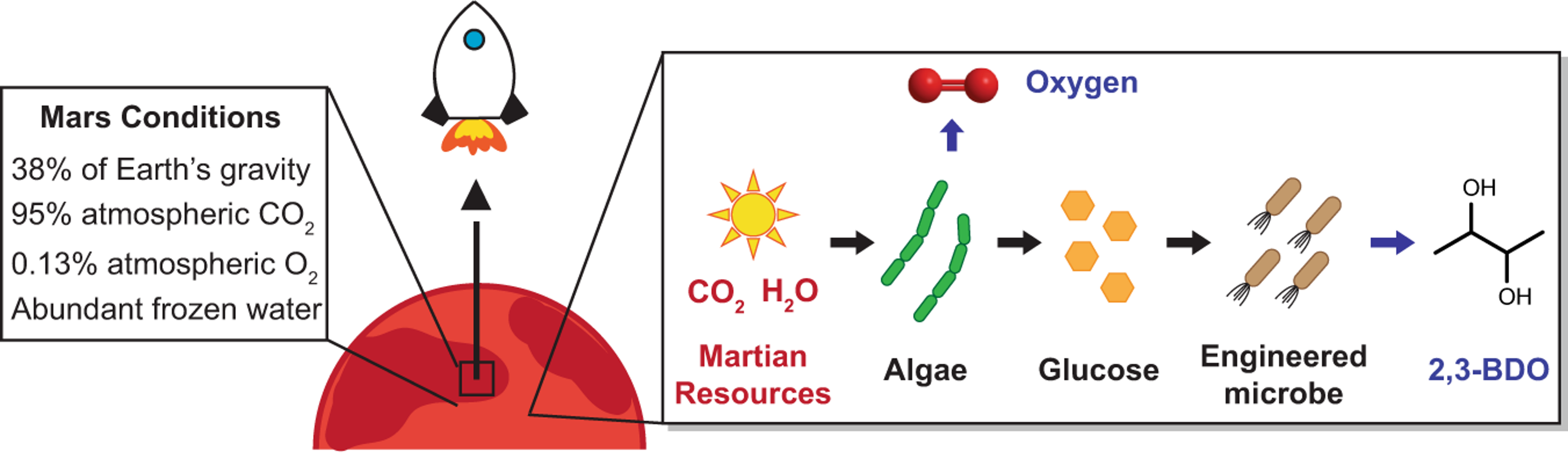
Comprehensive understanding of chemical kinetics is required to improve the design of combustion systems for both power generation and propulsion. For example, in the novel supercritical carbon dioxide power cycle, the combustor is operated at supercritical conditions with CO2 as diluent. Are chemical kinetics at these conditions the same or different from the conditions in conventional gas turbine combustor? Are existing kinetic models suitable (or not) for supercritical CO2 conditions? Detailed investigations are needed to answer these questions.
In the BTZ combustion lab, we use state-of-the-art facilities and diagnostics to investigate combustion kinetics. These facilities include a high pressure shock tube and rapid compression maching for autoignition and speciation, and various burners for flame speeds. Most notably, the 6-inch inner diameter and 66 ft long Georgia Tech high pressure shock tube is certified to operate up to 376 atmospheres. The shock tube creates a high-pressure and high-temperature environment "instantaneously", after which different diagnostics techniques -- such as chemiluminescence and laser absorption spectroscopy -- are applied to measure autoignition delays and quantify the production and consumption of certain species. These data can be used for kinetic model development and validation.
Below is an example of autoignition ignition delay measurements of methane (CH4) at supercritical CO2 conditions. The experimental data are then compared with numerical simulations. The performance of different kinetic models is clearly demonstrated with the help of new experimental results. (ref: Karimi, M., Ochs, B., Liu, Z., Ranjan, D., & Sun, W. (2019). Measurement of methane autoignition delays in carbon dioxide and argon diluents at high pressure conditions. Combustion and Flame, 204, 304-319.)
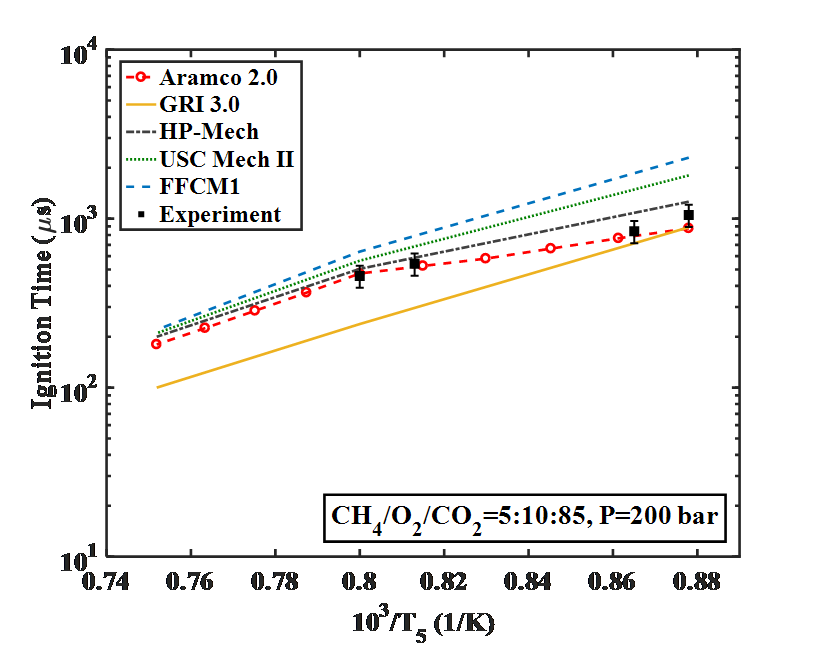
Another example is to design new fuels for deep space travel. For human presence beyond Earth to become a reality, we must not only send humans far into space, but also safely bring them back home. A key challenge for this vision is the origin of the fuel needed to bring spacecraft back to Earth. One idea is to develop human colony on Mars and use in situ resources on Mars to develop rocket propellants. We recently developed a methodology to produce 2,3-butanediol on Mars and we proved it to be suitable rocket propellants on Mars. (ref: Kruyer, N. S., Realff, M. J., Sun, W., Genzale, C. L., & Peralta-Yahya, P. (2021). Designing the bioproduction of Martian rocket propellant via a biotechnology-enabled in situ resource utilization strategy. Nature communications, 12(1), 1-14.)
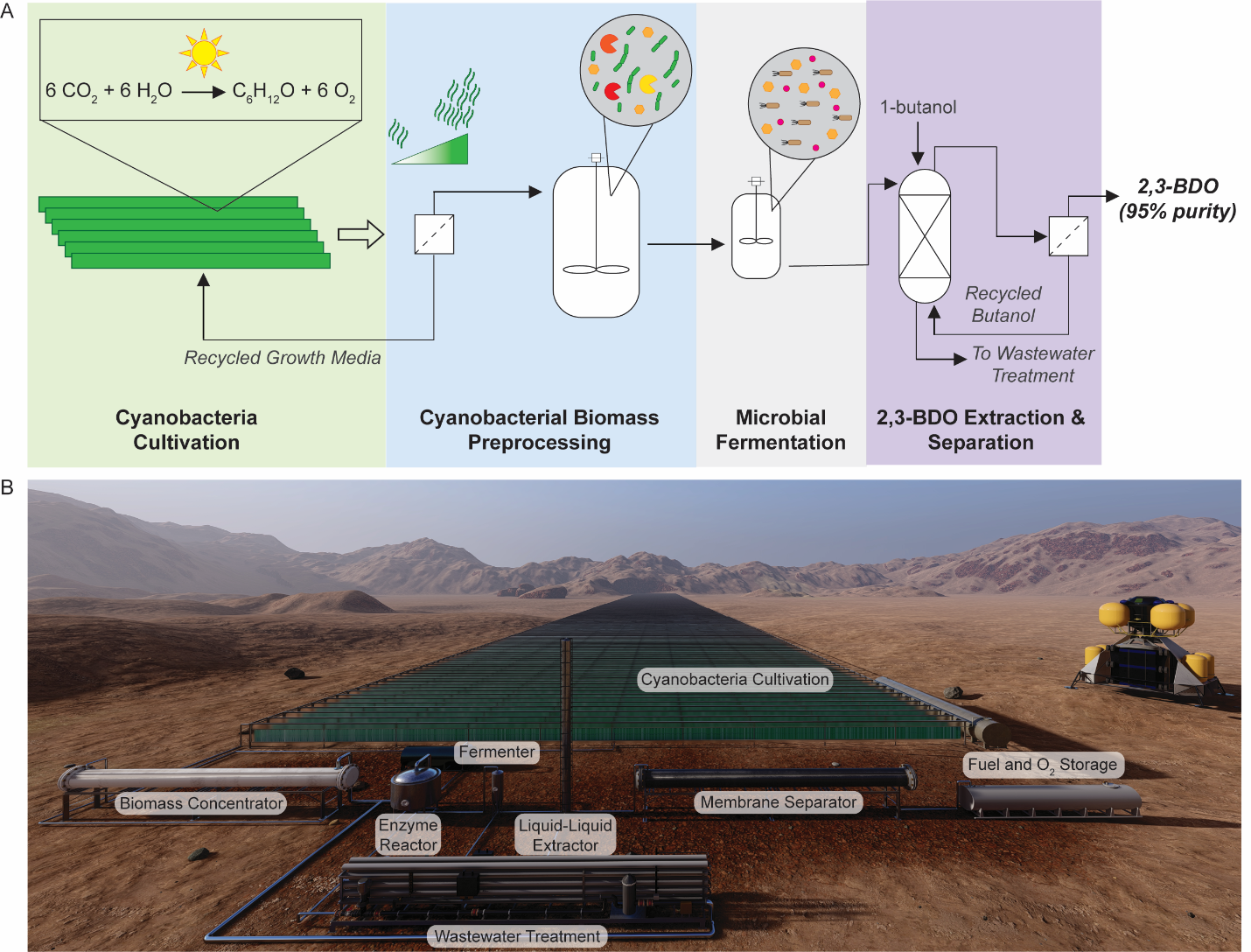